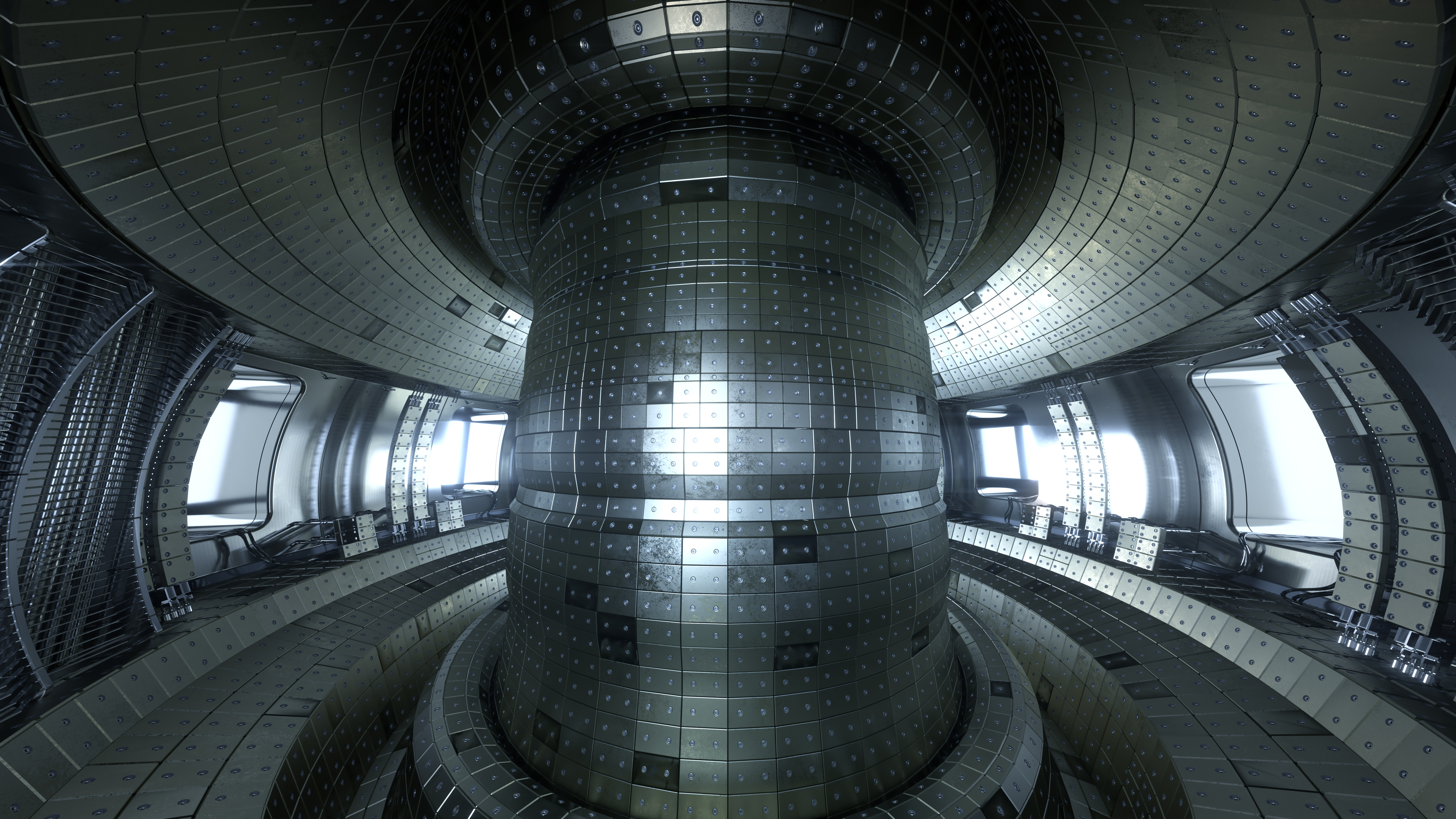
A traditional tokamak reaction chamber inside a nuclear reactor
How is it possible to protect superconducting magnets at -250°C from a fusion plasma at over 100 million degrees?
It turns out that scientists at UNSW Engineering have the answer and Tokamak Energy, a UK company developing commercial fusion energy, is excited about the technology.
Tokamak Energy is one of the world-leaders in the race for commercial fusion energy. The company is combining novel and robust high temperature superconducting magnets with the highly efficient and well-proven design known as a ‘Spherical Tokamak’.
One of the key challenges in a Spherical Tokamak for fusion energy is that the radiation shielding system, which protects the HTS magnets in the Central Column from heating and damage, needs to be as thin as possible. Simulations show that Tungsten Borides are likely to be highly effective.
Tokamak Energy and UNSW Sydney are delighted to announce a research project to understand the precise mechanisms of radiation damage in Tungsten Borides and then alter the chemistry, microstructure, and other parameters of the material to maximise the lifetime of the shield without sacrificing its shielding efficiency. These new materials will then be tested in a follow-on phase to the project, while the supply chain is engaged to produce the materials in the required volume.
Dr Patrick Burr, from the School of Mechanical and Manufacturing Engineering at UNSW, said: "I’m very excited about this new collaboration with Tokamak Energy. Together we’re going to accelerate the development of shielding materials for their spherical tokamak fusion power plant. It is a big challenge to protect superconducting magnets at temperatures close to absolute zero, from a fusion plasma hotter that the centre of the sun, but we can see how to do it."
Jack Astbury, Radiation Shielding Team Leader, from Tokamak Energy said: "It is great to be working with Patrick and his UNSW colleagues to tackle this crucial challenge for fusion power plants. Optimising the shielding materials will allow us to make quicker progress and will lead to lower cost – and much more economically viable – devices."