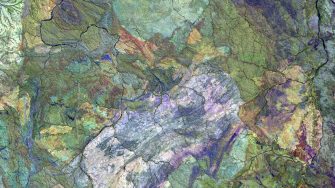
We don’t want engineering materials to fail because they can cause loss of life, economic loss or a loss of products or services. The usual causes of material failure are incorrect materials selection, incorrect processing, incorrect manufacturing procedures, inadequate design or incorrect use. Fracture is the separation of a body into two or more pieces as a result of an imposed stress.