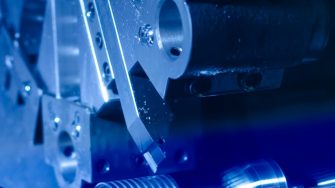
Developing new alloys and processes for transportation, infrastructure, electronics and biomedical applications
Using state-of-the-art facilities, we are developing new types of alloys with outstanding properties for various applications of direct benefit to society. All projects involve the production all our own materials either at UNSW or in our industry partners’ labs. These materials are produced by standard methods (such as casting and thermomechanical processing) through to more advanced methods of direct strip casting, spark plasma sintering, thin film deposition and 3D laser printing (additive manufacturing) for generating as-cast, thermomechanical processed, near-net-shape, and net-shape final products.
Various advanced processing and characterisation techniques are available for understanding the structure and properties including, for example, Gleeble 3500 TMP simulator, melt spinner, arc melters, 3D printers, hot and cold rolling mills, twin roll strip caster, magnetron sputtering, spark plasma sintering, scanning electron and transmission electron microscopy, focused ion beam microscopy, differential scanning calorimetry, and X-ray diffraction etc. Some examples of our current projects are highlighted below:
Design of ultra-lightweight alloys
Our recently discovered ultra-light magnesium alloys are not only exceptionally strong and ductile, but corrosion resistant. As such, this new class of ‘stainless’ magnesium alloy has generated considerable interest for use in the automotive, aerospace, biomedical, sporting and electronic goods sectors. We are unravelling the reasons for the corrosion resistance of these alloys, why they are both strong and ductile, and how we can further improve their properties. The latter involves alloy design strategies for creating new compositions through to advanced structural characterisation for understanding their unique structures and properties.
Agile manufacturing routes for creating novel alloy structures
Advanced materials are vitally important, but it is often the actual processing method that generates the novel structure/property combinations. We are working on innovative manufacturing/processing routes for generating near-net-shape and net-shape final products exhibiting unique structures and properties. These processing routes are very versatile and generally classed as ‘green-processes’ due to their minimal impact on the environment. We are focusing on methods such as thin film deposition, die casting, direct strip casting and additive manufacturing for generating new types of alloys without the need for major further processing. Materials of interest include advanced structural steels, aluminium, magnesium, copper and titanium alloys, and new classes of high entropy alloys.
Design of implantable biomedical alloys
We are developing new glassy alloys and crystalline high entropy alloys that are as strong as steel but also biocompatible with the human body. Some can also be formed like a thermoplastic polymer into the desired shape by the surgeon followed by implanting. The novelty lies in the ability to tailor an alloy’s composition for creating either bio-inert or biodegradable alloys. The latter are particularly useful as bone fixation devices as they degrade gradually without trace, thereby eliminating the need for further intrusive surgery to remove the material once the bone is healed.
Group leader
Research group
Current researchers
- Dr Martin Xu – Physical metallurgy and advanced processing
- Dr David Miskovic – Physical metallurgy and advanced processing
- Dr Reza Mahjoub – Ab initio molecular dynamics simulations
- Yiyao Wang (PhD) – Structure and properties of ultralight magnesium alloys
- Aidong Xu (PhD) Jointly with Prof Jinfu Li, SJTU – Formation and control of eutectic structures
- Michael Dela Cruz (PhD) Jointly with Xiaopeng Li, Mech Eng – Additive manufacturing of shape memory alloys
- Zhenyu Wang (PhD) Jointly with Xiaopeng Li, Mech Eng – Additive manufacturing of Ti-base biomedical alloys
- Hui Kong (PhD) Jointly with Xiaopeng Li, Mech Eng – Additive manufacturing of high entropy alloys
- Hao Su (MSc) – Structure and properties of ultralight magnesium alloys
- Qijing Sun (PhD) – Ultrastable thin film metallic glasses
- Thomas Xin (PhD) – Spinodal strengthening in magnesium lithium alloys
Recent student completions:
- Song Tang (PhD, 2020) – Unique property profiles in magnesium lithium alloys
- Li Xianchao (PhD, 2019) – Thermomechanical processing of duplex stainless steels
- Yu Chen (PhD, 2019) – Structure and properties of in situ metallic glass composites
- Caitlin Healy (PhD, 2018) – Development of precious metal high entropy alloys
- Scott Gleason (PhD, 2018) – Biocompatible metallic glass thin films
- Nicholas Hamilton (PhD, 2017) – Ab initio MD simulations of metallic glasses
- Patrick Conway (PhD, 2017) – Development of lightweight high entropy alloys
- Lance Tang (PhD, 2017) – High specific strength and corrosion resistant magnesium alloys
- Michael La Robina (PhD, 2017) – Extreme temperature materials
- David Miskovic (PhD, 2016) – Biocompatible MgZnCa metallic glasses
- Jiaqi Duan (PhD, 2016) – Roll bonding and grain stability of low solute alloys
- Jacky Cao (PhD, 2015) – Synthesis of Al-based metallic glasses
- Karl Shamlaye (PhD, 2014) – Processing and properties of BMG composite sheets
- Fitri Wahid (PhD, 2014) – Production and properties of Al-based metallic glasses
- Olga Biletska (PhD, 2014) – Lightweight in situ BMG composites
- Nasima Afrin (PhD, 2013) – 3D-EBSD of deformation microstructures
- Jake Cao (PhD, 2013) – Processing and properties of biocompatible metallic glasses
- Gregory Guo (PhD, 2012) – Processing and properties of multifunctional Ti-Nb-O alloys
- Oday Al-Buhamad (PhD, 2010) – Microstructure and properties of multilayered Al alloys